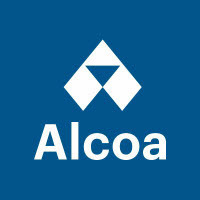
Description
Shape Your World
At Alcoa, you will become an essential part of our purpose: to turn raw potential into real progress. The way we see it, every Alcoan is a work-shaper, team-shaper, idea-shaper, world-shaper.
About the Role:
This position is accountable for providing direction and managing the activities of the Smelting Maintenance Supervisors and bargaining unit employees in Maintenance. The principal challenge is to provide leadership that is aligned with Plant and Departmental operating plans in the areas of environment, safety & health (EHS), cost, Alcoa Business System (ABS), Asset Management (REX), quality, customer satisfaction and labor relations. The Flow Leader is the owner of the department training plan, employee training and ensuring that every employee is adhering to the quality and safety standards (SSOP's, process control computer to control quality, etc.). This position will lead the supervisors to meet the maintenance schedules for the location. The primary focus is to implement the plans crafted by members of the maintenance organization while always leading with Alcoa's priorities and values.
Key Responsibilities:
- Safety of our employees is the #1 goal. Support, promote, and enforce all EHS guidelines and practices.
- Use Human Performance (HP) tools and promote environmental values
- Ensure there is a robust training system in place that lines up with our HP and ABS principles.
- Ensure that all employees are performing work according to the correct safety standards and quality procedures (all SSOPs and SPL are being followed) via audits
- Participate in any labor relations issues within the maintenance department including the grievance and discipline processes.
- Accountability for departmental budgets, headcount, and work-hour management. Responsible for delivering and driving improvement on cost and volume productivity opportunities, work hours, headcount and other key performance:
- Maintain and foster positive employee relations and communications
- Execute the maintenance schedule in a timely and safe manner, while continuously striving to improve efficiency.
- Apply a continuous improvement attitude by aggressively evaluating new insights and approaches for maintenance cost reduction.
- Conduct Performance Management (PM) for direct reports provide mentorship continuously improve their skill level.
- Backfill for the Maintenance Manager
- Regularly interface with manufacturing customers to develop strong inter-departmental relationships. Champion the implementation of solid partnering relationships between maintenance and the production departments.
- Assist in developing maintenance budgets and tactical plans to meet Massena's objectives for the department.
- Advise and counsel subordinates on policy and procedure matters, handle suggestions and appraise work related problems in accordance with established policies and procedures. Responsible for all aspects of Performance Management for direct reports.
- Provide leadership in assisting the planning process in maintaining computerized equipment histories, maintenance cost records, equipment PMs and lube schedules, equipment spare parts' inventory, and other information related to asset management.
- Provide leadership in support of the maintenance reliability process and provide consultation to reliability engineering functions.
What you can bring to this role:
- Supervisory experience in a manufacturing or process industry.
- Excellent communication skills with proven track record to build relationships at all levels of the organization.
- Influential and flexible leadership with experience encouraging and championing a diverse workforce.
- Excellent analysis and problem-solving skills
- Combinations of education or military service and industrial manufacturing experience:
- 4-year degree and 2 years of industrial manufacturing leadership experience; or
- 2-year associates degree and 4 years of industrial manufacturing experience; or
- High school diploma or GED with 8 years of industrial manufacturing experience.
- Ability to influence and communicate across the spectrum of the workforce (i.e. management to operators and maintainers).
- 8 years of growing responsibility in an industrial manufacturing environment
- Strong verbal and writing skills
- Computer literacy; MS office and related packages. MS Excel is important.
- Results-Focused aptitude.
- Strong work ethic to deliver safe, clean and efficient maintenance.
- Strong communicator, ability to train others and speak in front of an audience.
- Must be self-motived and a problem solver.
About the Location
Our Massena facility in New York State, established in 1902, is home to the longest continuously operating smelter in the world. Located on the St. Lawrence River, Massena, NY is the center for commercial, industrial, and manufacturing success in St. Lawrence County. Massena's caring sense of community, affordable cost of living, and extremely low-cost locally supplied energy, coupled with four public and private universities nearby, make Massena a great place to call home. And within a two hour drive (or less) are cosmopolitan and historic Montreal and Ottawa, Canada to the north, and to the south are the tall, beautiful views of Adirondacks and within it is Lake Placid The Olympic Village.
We are values led, vision driven and united by our purpose of transforming raw potential into real progress. Our commitments to Inclusion, Diversity & Equity include providing trusting workplaces that are safe, respectful and inclusive of all individuals, free from discrimination, bullying and harassment and that our workplaces reflect the diversity of the communities in which we operate.
As a proud equal opportunity workplace and affirmative action employer, Alcoa is dedicated to providing equal opportunities and equal access to all individuals regardless of a person's gender, age, race, ethnicity, sexual orientation, gender identity, religion, nation of origin, disability, veteran status, language spoken or any other characteristic or status protected by the laws or regulations in the places where we operate.
If you have visited our website in search of information on U.S. employment opportunities or to apply for a position, and you require an accommodation, please contact Alcoa Recruiting via email at gssrecruiting@alcoa.com.
This is a place where you are empowered to do your best work, be your authentic self, and feel a true sense of belonging. Come join us and shape your career!
Your work. Your world. Shape them for the better.
Application close date is: 3 June 2025, however Alcoa reserves the right to change this date at its discretion.Apply on company website