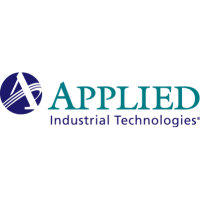
Description
The Commissioning, Qualification, and Validation Engineer, Engineer II and Senior Engineer report directly to the Team Leader, Manager, or Director of the CQV Team, depending on the organizational structure. These positions are exempt. Up to 50% travel may be required.
Expectations:
The CQV Engineer II performs commissioning, qualification, and validation testing on manufacturing process equipment and instruments, authors protocols, initiates controlled documentation, and provides client support for CQV projects either independently or as part of a larger team. Responsibilities may include generation of documents such as master plans, design qualification, equipment, facility and utility commissioning and development and development of final reports. The position requires extensive interaction with clients to identify CQV needs and work towards solutions that meet schedule, cost, and quality expectations and requirements. CQV Engineers take a proactive role in supporting CQV projects and in providing client support. They build a high level of trust with internal and client personnel. This trust is developed through consistently upholding PCI Values and demonstrating Integrity, Accountability, Unified Team (Teamwork), and Creativity (Innovation).
Responsibilities/Assignments:
CQV Engineer II
- Performs commissioning, qualification, and validation testing on utilities and manufacturing process equipment and instruments independently or with minimal assistance from others
- Authors, reviews and approves protocols
- Initiates and reviews controlled documentation for final approval and provides client support for CQV projects independently or with minimal assistance
- Develops and reviews documents such as master plans, design qualification, equipment, facility and utility commissioning and final reports
- Interacts with clients to identify CQV needs. Plans, recommends and implements solutions that meet schedule, cost, and quality expectations and requirements based on Good Engineering Practices
- Reviews equipment specifications, manuals, and has an in-depth understanding of how systems, equipment and instruments work. Tests equipment accurately to meet requirements for intended use. Identifies solutions to system, equipment and instrument issues
- Initiates failure and deviation investigations and reports. Recommends corrective actions and solutions
- Develops spare parts lists to ensure they are fit for purpose. Recommends critical spare part requirements and levels with the assistance of the Sr. CQV Specialist or Sr. CQV Engineer
- Reviews engineering drawings for accuracy and acts to correct errors independently or with minimal assistance
- Leads teams to perform system walk-downs and initiates the change control processes
- Initiates investigations and develops Corrective and Preventative Actions to clients to resolve CAPAs independently or with minimal assistance
- Develops and reviews summary and analyses reports independently or with minimum assistance
- Creates and maintains job plans, maintenance schedules and PMs independently or with minimal assistance
- Initiates projects independently or with minimal assistance. Provides direction and execution instructions to team members and follows up on project deliverables to ensure project success
- Identifies and documents scope changes and obtains approval from customers before execution
Skills Required:
CQV Engineer II
- In-depth understanding of cGMPs and pharmaceutical and biopharmaceutical unit operations. Reviews requirements and enforces procedures to ensure cGMP and regulatory compliance
- Possesses an in-depth understanding of principles, practices and procedures for commissioning and qualification. Can develop commissioning test plans independently or with minimal assistance
- Excellent analytical, organizational, time management and problem-solving skills. Can develop problem statements, identify root causes and create corrective actions to be executed within a prescribed timeline independently. Assists junior associates in developing analytical, organizational, time management and problem-solving skills
- Experienced writer. Develops and executes DQ, FAT, SAT, CTPIQ, OQ, PQ, and PV documents, develops SOPs, creates final reports and authors validation and quality policies, procedures and guidelines independently or with minimal supervision. Reviews documents developed by junior members. Ensures documents are accurate and compliant
- In-depth understanding of working in a construction environment with knowledge, skills and abilities to adhere to current industry guidelines, standards and safety requirements. Possesses OSHA 10 or higher certification
- Highly proficient at reading and interpreting P&IDs. Works with Sr CQV Engineer to correct as-built drawings
- In-depth understanding of and ability to apply GMP, GCP, GLP, GAMP and CFR21 Part 11 guidelines to ensure compliance as they relate to qualification of systems and validation of processes. Develops programs and procedures to comply with regulatory requirements.
- Highly skilled with Microsoft Word, Excel, PowerPoint, Visio and Project. Can create formulas, change formatting and develop professional presentations to help monitor and control project execution and to develop project status reports
- Leads project teams. Plans, organizes, monitors and controls project activities to ensure the project is on schedule, within scope, within budget and is meeting customer expectations.
- Highly experienced with validation in the following areas: manufacturing and utility systems, CIP & SIP, autoclave validation, qualification of controlled temperature environments, process validation, cleaning validation, equipment qualification, and use of the Validator 2000, Ellab E-Val Pro or other validators and various temperature and relative humidity loggers. Identifies client requirements and develops, routes for approval and executes validation protocols, including IQ, OQ and PQ documents
- Detail oriented with ability to plan, organize and communicate CQV project tasks across a multidisciplinary team. Reviews work efforts and documentation to ensure accuracy. Provides training to reduce errors and improve accuracy
- Leads teams and provides direction to others
Experience & Education Required for CQV Engineer II:
BS in Engineering, two years of relevant project experience and six years of applicable (Commissioning, Qualification, or Validation) experience or the equivalent combination of education and experience. In-depth knowledge of Quality System and the Life Science manufacture industry is required. Understands and follows all regulatory requirements, Engineering Best Practices and ISPE Good Practices
Or
MS in Engineering, two years of relevant project experience and four years of applicable (Commissioning, Qualification, or Validation) experience or the equivalent combination of education and experience. In-depth knowledge of Quality System and the Life Science manufacture industry is required. Understands and follows all regulatory requirements, Engineering Best Practices and ISPE Good Practices
PCI is proud to serve pharmaceutical, biotechnology, medical device, and clinical research industries nationwide by providing calibration, commissioning and consulting solutions. At PCI, calibrations are performed by highly technical, cGMP/GLP-trained personnel who are knowledgeable in quality guidelines enforced by the FDA, EPA and ISO/IEC 17025:2017. PCI is an FCX Performance Company and a Subsidiary of Applied Industrial Technologies (NYSE: AIT); a leading industrial distributor that offers more than 6.5 million parts to serve the needs of MRO and OEM customers in virtually every industry.
Applied® provides engineering, design and systems integration for industrial and fluid power applications, as well as customized mechanical, fabricated rubber and fluid power shop services. Applied also offers storeroom services and inventory management solutions that provide added value to our customers.
We are an equal employment opportunity employer. All qualified applicants will receive consideration for employment without regard to race, color, religion, national origin, ancestry, gender, sexual orientation, gender identity, age, disability, protected veteran status, marital status, medical condition or any other characteristic protected by law.
Apply on company website