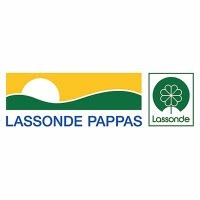
Description
SIGN-ON BONUS!
This position is eligible for a $2,500 sign-on bonus.
Want to learn how to make juice? Lassonde Pappas & Co. is a US Leader in beverage manufacturing dedicated to our team members, customers and consumers satisfaction. We remain committed to our small-town roots and rural values. Hardworking and caring are qualities that make our teams special. Since 1942, we've been producing delicious products for our customers across the country!
To provide the best for our customers, we focus on building the best team by creating and advancing an inclusive environment amongst our diverse workforce. If you're passionate about customer satisfaction, reliable, and committed to being and doing better, join us!
We value each of our employee's total wellbeing. To support employees in all stages of their wellness journey, we have a robust benefits program including: medical, dental, and vision coverage options, growth and development potential, along with 401-K, Life & Disability Insurance, PTO, Tuition Reimbursement, Health Fairs, Gym Membership Discounts, and so much more!
POSITION SUMMARY
The Production Supervisor oversees and coordinates the work of line employees. The primary responsibility of the Production supervisor is to provide the Maintenance and Operations Department with support in the areas of systems development, cost control, operational training, capital project management, business expenses; as well as, safety, environmental, and health issues. This position is also responsible for maintaining assigned areas for Food Safety and Food quality along with audit compliance and reporting. This role reports to the Production Manager and is based out of our Hendersonville, North Carolina location.
Shift: 10pm-6:30am
Primary Responsibilities include:
- Troubleshoot equipment individually and through coaching of the operators when there is downtime. Assist operators in resolving mechanical and operational issues related to equipment stops and breakdowns.
- Work with the operations department to facilitate a teamwork approach, combining the expertise and manpower of both production and maintenance departments for the good of the company
- Manage work area to maintain food safety and quality along with audit compliance and reporting
- Define project priorities and provide direction to production staff. Monitor team performance and audit activities to ensure personnel are performing quality work, supporting a quality product, and managing equipment to meet goals.
- Provide leadership to the team which includes following the Performance Management System, setting expectations that align with the area's business objectives, and providing routine feedback on performance.
- Manage the PDCA process from cradle to grave to include a problem statement, root cause analysis, and countermeasure implementation.
- Work with improvement teams to identify, evaluate, and implement reliability improvement opportunities through changes to operating procedures, maintenance procedures, and equipment upgrades.
- Develop, post, and communicate procedures/processes for their area that support the production strategies.
- Utilize preventive and predictive operator maintenance techniques to minimize equipment breakdowns
- Manage personnel plan to set up team for success.
- Develop and implement operator preventative maintenance systems. Maintains the plant CIL program, Changeover Program, Startup/Shutdown procedures, and Machine Centerline process.
- Assist in the selection process of new hires. Manage the production training program for the production staff.
- Ability to understand line control, bottle flow, and can flow to balance the line so the flow of work is at an even pace.
- Ability to understand staffing and productivity calculations to understand measures and set targets.
- Coordinate with the maintenance department to drive optimum performance on production lines, and assist with supporting production personnel as needed.
- Ability to analyze data with the use of the computer so measures and set targets can be communicated.
- Demonstrate a working understanding and ability to operate all plant machinery.
- Possess the ability to troubleshoot machine setup issues and operator competency gaps.
- Capability to develop training standards and work instructions for production processes.
- Train new employees that are hired in the work area assigned
- Advanced knowledge of the field
- Lead by example and assist others who may need guidance
- Be accessible for employees to ask questions regarding areas of expertise
- Provide positive recognition to employees who exhibit good behavior in their work area
- Provide feedback to managers on individual and team performance
- This role will be required to taste test products as needed, up to a couple of ounces per test
- Performs other related duties as required and assigned
SUPERVISORY RESPONSIBILITIES (If applicable)
- Manage multiple employees; the Production Team reports to this position.
- Monitor employee productivity and provide constructive feedback, coaching, counseling, and disciplining; conducting training; implementing enforcing systems, policies, and procedures.
- Maintains professional and technical knowledge by attending educational workshops; reviewing professional publications.
- Communicates job expectations; planning, monitoring, and assessing job results; coaching, and counseling employees; developing, coordinating, and enforcing systems, procedures, and productivity standards.
- Establishes strategic goals; identifying and evaluating trends; choosing a course of action; defining objectives; evaluating outcomes.
- Lead and support a food safety and food quality culture within the location
- Establish, document, and communicate to all relevant staff of food safety and quality objectives and performance measure
- Empower and encourage employees to act to resolve food safety and quality issues within their scope of work
- Implement, maintain, and continuously improve the food safety and quality culture within the location
- Effectively communicate all key performance indicators and objectives to employees
- Ensure staffing and adequate resources are maintained to meet objectives
- Educate all staff to understand the importance of food safety and food quality controls and deviation consequences.
EDUCATION AND EXPERIENCE
Minimum Required Qualifications
- High School Diploma, GED, or equivalent required;
- College degree or equivalent strongly preferred.
- 3-5 years previous experience in Manufacturing or a production environment.
- Must have experience using a PC and business information systems/software.
Additional Preferred Qualifications
- Experience in the food/beverage industry
- Experience in writing reports and KPI's
- Must have excellent verbal and written communication skills
- Must be detailed oriented and have the ability to multi-task
- Must have excellent time management skills
- Ability to direct, coach and train others.
- Consultative, influential, strategic thinking and problem-solving skills.
PHYSICAL REQUIREMENTS, SUPERVISORY RESPONSIBILITIES & WORKING CONDITIONS
This position requires sufficient physical ability to work in a typical manufacturing setting.
FREQUENT: Ability to talk and hear; ability to stand, walk, climb stairs, stoop, bend and/or crouch; push/pull; lift up to 50 pounds; use of hands and fingers to operate machinery/equipment and all manual and electronic equipment in area of responsibility. Exposure to wet and humid conditions and fluctuations in ambient temperature (seasonal).
OCCASIONAL: Squatting, kneeling, ability to reach above and at shoulder height. Ability to wear a dust mask, and perform Confined Entry using LOTO program. Exposure to toxic and corrosive chemicals.
VISION: Ability to use close and distance vision, as well as color and peripheral vision with or without correction. Must be able to visually detect obstacles and potential dangers in a fast-paced production environment involving high speed equipment and powered industrial lift equipment.
HEARING: Ability to hear in the normal audio range with or without correction. Exposure to noise levels from pumps, machinery, forklift traffic, bottle lines and exhaust fans.
This job description is not intended to contain a comprehensive list of the responsibilities that are required to successfully perform in this position. Other duties as assigned are part of every job description. The conditions herein are representative of those that must be met by an employee to successfully perform the essential functions of this job. Reasonable accommodations may be made to enable individuals to perform the essential job functions.
Lassonde Pappas & Co., Inc provides equal employment opportunities to all employees and applicants for employment and prohibits discrimination and harassment of any type without regard to race, color, religion, age, sex, national origin, disability status, genetics, protected veteran status, sexual orientation, gender identity or expression, or any other characteristic protected by federal, state or local laws.
This policy applies to all terms and conditions of employment, including recruiting, hiring, placement, promotion, termination, layoff, recall, transfer, leaves of absence, compensation and training.
Apply on company website